Objective Heating a titanium fastener to 1100-1450ºF (593-788ºC) for an annealing process.
Material 0.06” (1.5mm) high zone on a titanium fastener measuring 0.163-0.375” (4.14-9.52mm) in diameter and 0.5-3.0” (12.7-76.2mm) in length
Temperature 1100-1450ºF (593-788ºC)
Frequency 125 kHz
Equipment • 25 kW induction heating system, equipped with a remote workhead containing one 0.66μF capacitor.
• An induction heating coil designed and developed specifically for this application.
Process A three turn concentrator plate coil is used to heat the fastener
for 0.2 seconds. This is an automated process that includes robotic placement of parts in the coil from a bowl fed track while Argon gas is flooded across the part to prevent oxidation.
The parts are processed at a rate of 1000 parts per minute.
Results/Benefits Induction heating provides:
• Can be incorporated easily with pick and place robotics.
• Flameless process.
• Heating is limited to the specific area
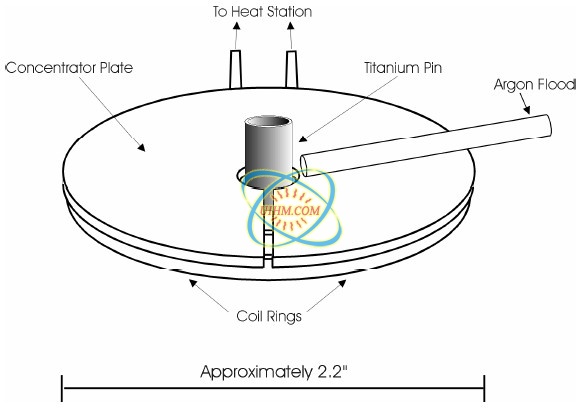
Material 0.06” (1.5mm) high zone on a titanium fastener measuring 0.163-0.375” (4.14-9.52mm) in diameter and 0.5-3.0” (12.7-76.2mm) in length
Temperature 1100-1450ºF (593-788ºC)
Frequency 125 kHz
Equipment • 25 kW induction heating system, equipped with a remote workhead containing one 0.66μF capacitor.
• An induction heating coil designed and developed specifically for this application.
Process A three turn concentrator plate coil is used to heat the fastener
for 0.2 seconds. This is an automated process that includes robotic placement of parts in the coil from a bowl fed track while Argon gas is flooded across the part to prevent oxidation.
The parts are processed at a rate of 1000 parts per minute.
Results/Benefits Induction heating provides:
• Can be incorporated easily with pick and place robotics.
• Flameless process.
• Heating is limited to the specific area
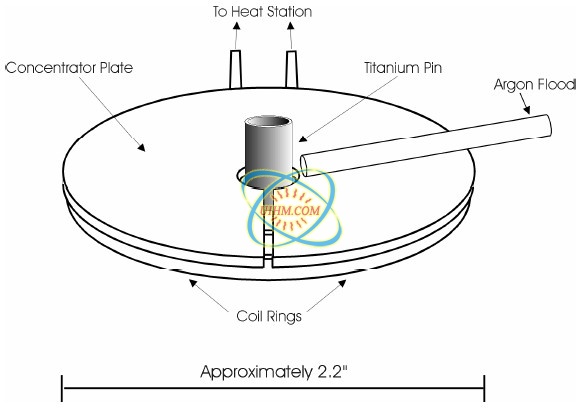
Newest Comment
No Comment
Post Comment