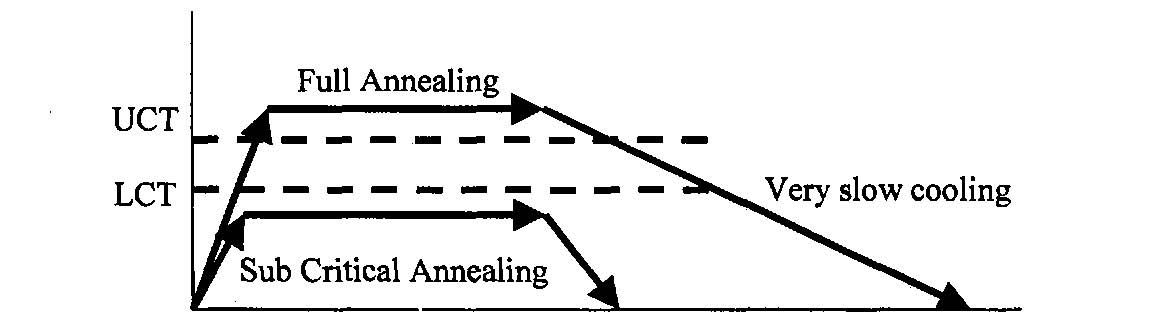
HEAT TREATMENT
We use heat treatments to change properties of metal, or as a method of controlling formation of structures, or expansion/contractional^forces during welding. In heat treating metals and alloys there are many elements for the welding inspector to check that may be of great importance, such as the rate Of climb and any hold points in the heating cycle. The holding or soaking time is generally calculated at lhour for every 25mm of thickness* but this can vary. Heat treatments that are briefly covered in this section are as follows: 1) Annealing 2) Normalising 3) Hardening 4) Tempering 5) Stress relieving 6) Pre-heating The methods/sources that may be used to apply heat to a fabrication may include:
a) Flame burners/heaters (Propane etc.) Preheating
b) Electric resistance heating blankets. Pre-heating & PWHT
c) Furnaces. Annealing. Normalising. Hardening. Tempering
The tools that an inspector may use to measure the temperatures of furnaces and heated materials may include.
a) Temperature indicating crayons (Tempil sticks). Pre-heating
b) Thermo-couples. All heat treatments.
c) Pyrometers (Optical. Resistance. Radiation.). Furnace heat treatments
d) Segar cones. Furnace heat treatments
The welding inspector should observe that all heat treatments are carried out as specified and make records of all parameters. This is a critical part of the duties of a welding inspector who should also ensure that all documents are retained within the quality files.Annealing is a heat treatment process that may be carried out on steels, and most metals that have been worked hardened or strengthened by an alloying precipitant, to regain the softness and ductility. In the latter case we generally refer to solution annealing. In work hardened non-ferrous metals, annealing is’used to re-crystallise work-hardened grains. When annealing most work hardened non-ferrous alloys the cooling rate is not always critical, and cooling may be rapid without forming any hardened structures. In steels we can carry out 2 basic kinds of annealing:
a) Full Annealing (Including Solution Annealing)
b) Sub Critical Annealing
In full annealing of steels the steel is heated above its UCT (upper critical temperature) and allowed to cool very slowly in a furnace. This slow cooling will result in a degree of grain growth, which produces a soft and ductile structure. There are no temperatures that can be quoted for annealing steels, as this will depend entirely upon the carbon content of the steel.
The UCT range of Plain Carbon Steels ranges between 910 – 723 °C, however the temperature Us mostly taken to 50 °C above the calculated UCT to allow for any inaccuracies in the temperature measuring device. Plain carbon steel of carbon content of 0.2% would have an annealing temperature in the region of 850 – 950 °C
The solution annealing of some metallic alloys may require a rapid cooling rate.
In sub critical annealing the steel is heated to temperatures well below the lower critical temperature (723 °C). This type of annealing is similar to that used with non-ferrous metals as it is only the deformed ferritic grains that can be re-crystallised at these lower temperatures.
The term annealing generally means to bring a metal, or alloy, to its softest and most ductile natural condition. In steels this also means a reduction in toughness, as the resultant large grain structure shows very low impact strength-
2) Normalising
Normalising is a heat treatment process that is generally used for steels. The temperature climb and holding may be exactly the same as for annealing, however the steel is removed from the furnace after the soaking period to be allowed to cool in still air. This produces a much finer grain structure than aijnealing and although the softness and ductility is reduced, the strength and hardness is increased. Far more importantly the toughness, or impact strength is vastly improved.
3) Hardening
In the thermal hardening of steels the alloy must be taken above its UCT as with all the heat treatment processes discussed thus far, and soaked for the same period. The major difference is in the cooling cycle where cooling is generally rapid. For plain carbon steel, the steel must have a sufficiently high carbon content to be hardened by thermal treatment, which is generally considered as > 0.3% carbon. Alloy steels containing carbon contents below 0.1% with lidded Mn. Cf. Mo. or Ni. Etc. can be made much harder by thermal heat treatment. Some steels are specially designed to produce hardness even at very slow rates of cooling, and are included in a group of steels called Air Hardening Steels. The cooling media for quenching steels is very important; as if the steel is cooled too quickly then the thermal shock may be too rapid and cause cracking to occur in the steel. Brine is considered to be the fasted cooling media followed by water and then oil.
HEAT TREATMENT.PDF
Newest Comment
No Comment
Post Comment