Objective Soldering steel onto GPS body for phone antenna
Material Thin copper foil 0.3mm (0.01 in) thick Ceramic body 12mm (0.47 in.) long x 7mm (0.28 in.) wide
Temperature 200º C (392º F)
Frequency 371 kHz
Process Time 5 seconds
Equipment • Power of 6 kW induction heating system, equipped with a remote workhead containing (2).33μF capacitors (for a total of .66 μF).
• Two coils (one for each stage of process) designed and developed specifically for this application. The first stage uses a two-turn solenoid coil with a 15mm (0.6 in) ID and the second stage uses a plate coil, 25
mm (1 in.) dia. with a 6mm (0.24 in.) hole.
Process
Stage 1: A two-turn solenoid coil is used to heat the top end of a GPS antenna. Solder paste is used to solder the walking stick loop to the copper foil.
Stage 2: A plate coil is used to heat the bottom part of the GPS to solder a top hat to the copper foil and also the bottom part of the walking stick.
Results/Benefits Induction heating benefits:
• increased production rate due to speed of heating
• higher quality vs. a soldering iron due to precision and repeatability
• cost savings due to reduced scrap and higher quality production
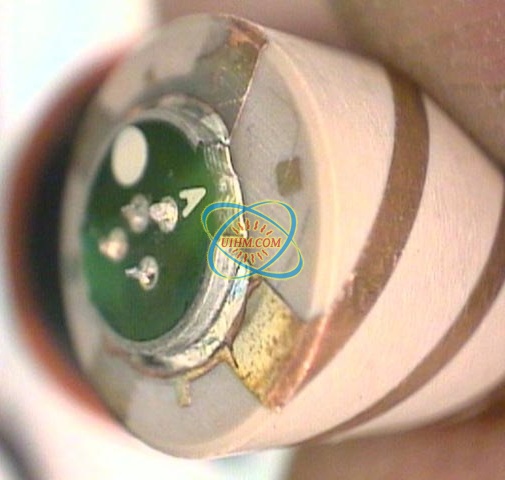
Soldering satellite antennas
Newest Comment
No Comment
Post Comment