Induction Shrink Fitting
Views Send Enquiry
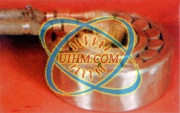
Induction Shrink Fitting is a procedure in which heat is used to produce a very strong joint between two pieces of metal, one of which is inserted into the other. Heat is applied to one of the pieces so that it expands, the other component is at ambient temperature. At this point the two pieces are placed one inside the other. As the hot component cools it contracts onto the already cool component producing interference and pressure which holds the two pieces together mechanically.
Features of the Induction Shrink Fitting technology:
Accurate and repeatable delivery of heat
Uniform heat giving predictable expansions
Precise control of cycle times
Reduced energy consumption
Fewer reject parts as all aspects of the process can be monitored
Ease of integration into an existing production cell
Better quality
Next: Induction Annealing Stainless SteelPrevious: Induction surface hardening
Good
Bad
Related Content
Air Cooled clamp coil (half-open coil) for preheating gas pipeline
induction coating by air cooled clamp induction coil
Remove plastic coating from steel tubes by Induction Heating
Releasing Fixture by Induction Heating
U shape air cooled induction coil by UM-100C-HF for pipeline preheating
induction quenching with custom-design inductor
induction brazing diamond segment
induction brass soldering copper plate_2
Hot
induction shrink fitting motor (stator or rotor)
induction installation (shrink fitting) couplings for Shaft Collar with flexible induction coil
induction shrink fitting wheel
induction shrink fitting stator
induction shrink fitting spindle
induction shrink fitting for rotor and stator
air cooled induction heating for fixing Nuclear Power Unit (loosen screw nut)
induction shrink fitting
Newest Comment
No Comment
Post Comment