Objective To heat the stainless steel substrate of a solar panel shingle in order to melt the polymer encapsulant, allowing two shingles to bond together with a 3 inch overlap.
Material 3″ by 10.25″ section of a 21″ solar panel shingle
Temperature 130 ºC
Frequency 166 kHz
Equipment Power of 20KW power supply equipped with a remote heat station containing one 0.66mF capacitor. A custom-made coil: 4 turns of 1/4″ x 1/2″ rectangular copper tubing, measuring
24″ by 2 1/4″.
Process Stationary heating – with the coil located on the topside of the sample – was utilized to achieve uniform melt and adhesion.
The shingles were overlapped according to requirements and placed on wood to simulate the installation on a roofing
surface. In addition, pressure was applied by pressing thewater-cooled coil against the shingle to facilitate the bonding (illustration). Tests are performed at several time-voltage settings.
Results Tests resulted in excellent bond formation with the absence of encapsulant bubbling and only slight surface texture change.
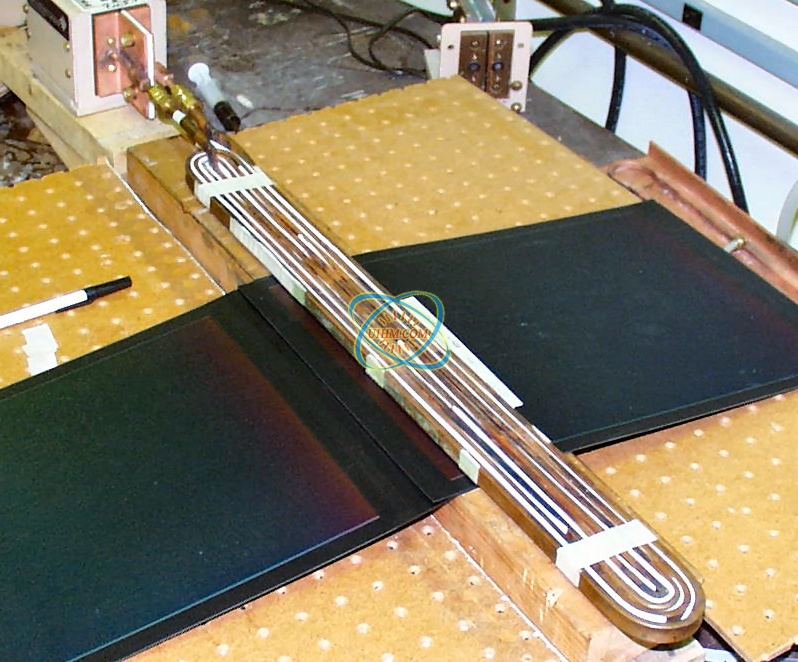
Material 3″ by 10.25″ section of a 21″ solar panel shingle
Temperature 130 ºC
Frequency 166 kHz
Equipment Power of 20KW power supply equipped with a remote heat station containing one 0.66mF capacitor. A custom-made coil: 4 turns of 1/4″ x 1/2″ rectangular copper tubing, measuring
24″ by 2 1/4″.
Process Stationary heating – with the coil located on the topside of the sample – was utilized to achieve uniform melt and adhesion.
The shingles were overlapped according to requirements and placed on wood to simulate the installation on a roofing
surface. In addition, pressure was applied by pressing thewater-cooled coil against the shingle to facilitate the bonding (illustration). Tests are performed at several time-voltage settings.
Results Tests resulted in excellent bond formation with the absence of encapsulant bubbling and only slight surface texture change.
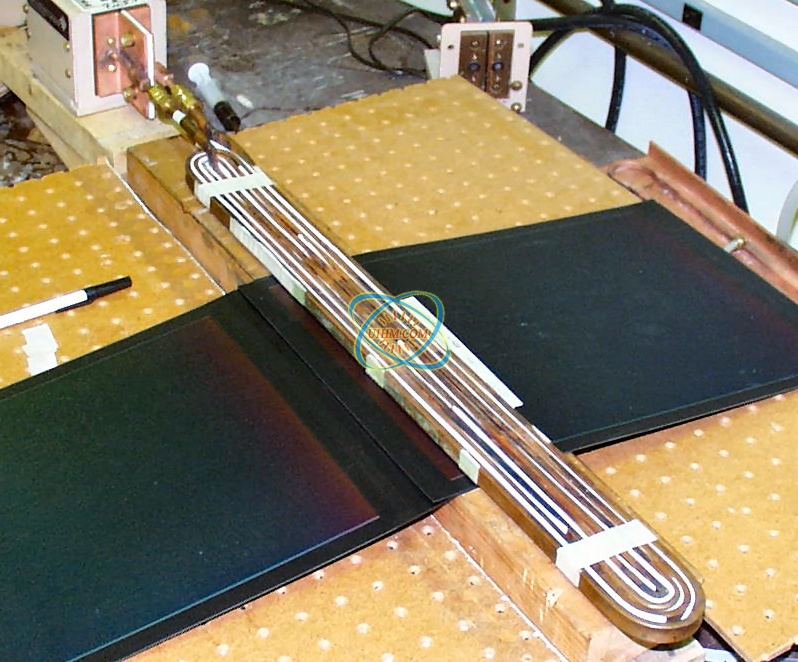
Newest Comment
No Comment
Post Comment