Surface Hardening of Steels
2013/4/8 Views
Selective hardening is applied because of one or more of the following reasons:
(1) Parts to be heat-treated are so large that conventional furnace heating and quenching become
impractical and uneconomical - examples are large gears, large rolls and dies;
(2) Only a small segment, section, or area of the part needs to be heat-treated-typical examples are
ends of valve stems and push rods, and the wearing surfaces of cams and levers;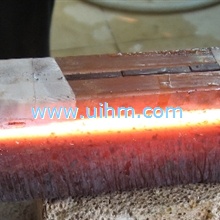
(3) Better dimensional accuracy of a heat-treated part; and
(4) Overall cost savings by giving inexpensive steels the wear properties of alloyed steels.
1. Flame Hardening
Flame hardening is the process of selective hardening with a combustible gas flame as the source
of heat for austenitizing. Water quenching is applied as soon as the transformation temperature is
reached. The heating media can be oxygen acetylene, propane, or any other combination of fuel
gases that will allow reasonable heating rates. For best results, the hardness depth is 3/16 inch.
There are three methods:
(1) Spot Flame Hardening: Flame is directed to the spot that needs to be heated and hardened.
(2) Spin Flame Hardening: The workpiece is rotated while in contact with the flame
(3) Progressive Flame Hardening: The torch and the quenching medium move across the surface
(1) Parts to be heat-treated are so large that conventional furnace heating and quenching become
impractical and uneconomical - examples are large gears, large rolls and dies;
(2) Only a small segment, section, or area of the part needs to be heat-treated-typical examples are
ends of valve stems and push rods, and the wearing surfaces of cams and levers;
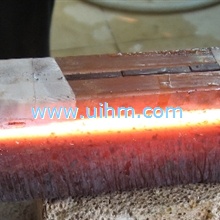
(3) Better dimensional accuracy of a heat-treated part; and
(4) Overall cost savings by giving inexpensive steels the wear properties of alloyed steels.
1. Flame Hardening
Flame hardening is the process of selective hardening with a combustible gas flame as the source
of heat for austenitizing. Water quenching is applied as soon as the transformation temperature is
reached. The heating media can be oxygen acetylene, propane, or any other combination of fuel
gases that will allow reasonable heating rates. For best results, the hardness depth is 3/16 inch.
There are three methods:
(1) Spot Flame Hardening: Flame is directed to the spot that needs to be heated and hardened.
(2) Spin Flame Hardening: The workpiece is rotated while in contact with the flame
(3) Progressive Flame Hardening: The torch and the quenching medium move across the surface
Down Attachment
- DownloadAttach1: Surface Hardening of Steels Surface .pdf Clicks
Good
(2)
100.0%
Bad
(0)
0.0%